Digital Twins: Revolutionizing Fatigue Component Qualification in Aerospace
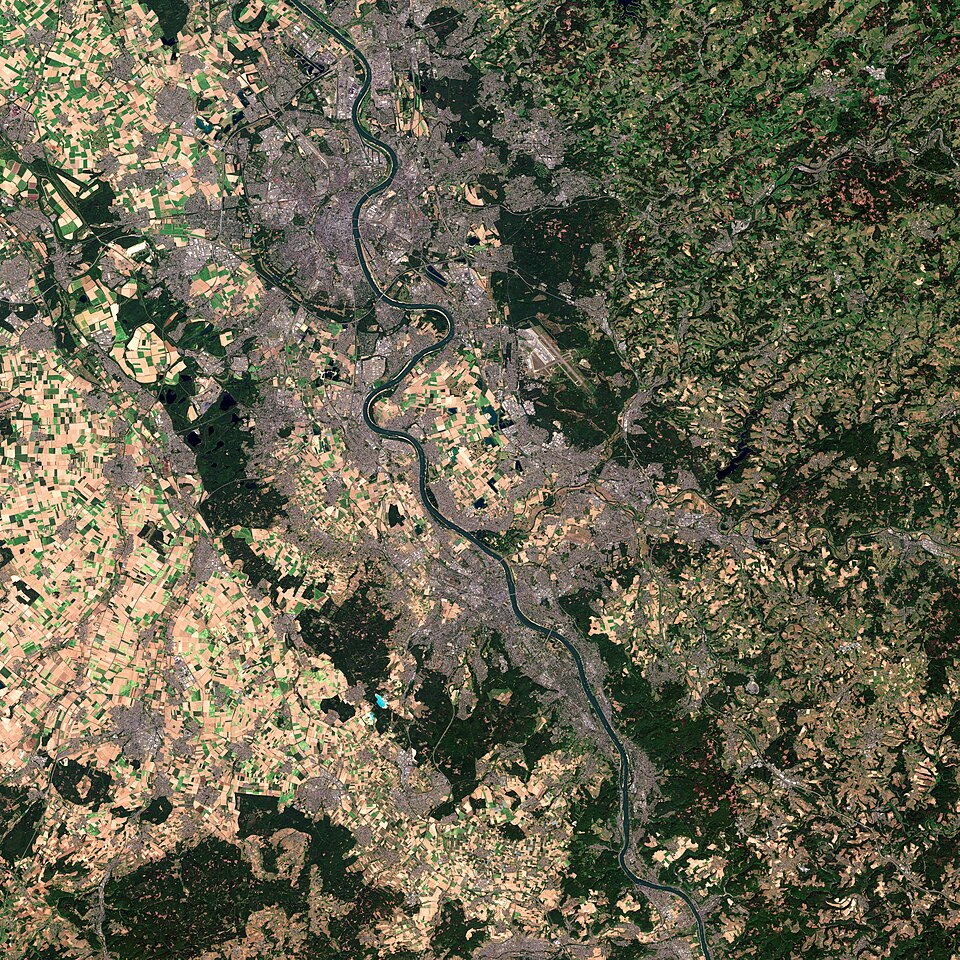
In the aerospace industry, fatigue failure poses significant challenges to the reliability and safety of components. Traditional qualification processes for fatigue-critical components are often lengthy and costly, requiring extensive testing to ensure compliance with regulatory standards. However, recent advancements in modeling technology, particularly through the use of digital twins and Integrated Computational Materials Engineering (ICME), are transforming the qualification landscape. This article explores how QuesTek's innovative ICMD® modeling software can accelerate the qualification of aerospace alloys, thereby enhancing efficiency and reducing costs.
The qualification process for aerospace materials is critical, as it involves demonstrating that components meet rigorous performance standards set by regulatory bodies such as the Federal Aviation Administration (FAA) and the European Union Aviation Safety Agency (EASA). According to Gary F. Whelan, a leading researcher and co-author of a white paper presented at the 31st International Conference on Aerospace Fatigue (ICAF) Symposium, the conventional methods of qualification are often labor-intensive and time-consuming. Whelan, alongside Jiadong Gong and Gregory B. Olson, emphasizes the need for innovative solutions that can streamline these processes.
QuesTek's ICMD® modeling software significantly reduces the reliance on extensive physical testing by leveraging physics-based simulations to predict material properties. This software incorporates both intrinsic factors, such as grain size and texture, and extrinsic factors, including porosity and surface roughness, which influence the fatigue life of materials. Dr. Sarah Johnson, Professor of Materials Science at Stanford University and an expert in computational materials engineering, notes that this approach allows for a more nuanced understanding of fatigue behavior, fostering quicker qualification timelines.
The framework developed by QuesTek combines crystal plasticity finite element methods with algorithms for small and long crack growth, enabling the prediction of fatigue life from initiation to failure. This integration of microstructure-informed digital twins facilitates a calibration process that aligns simulated results with experimental data, thereby providing a more accurate representation of real-world conditions.
Furthermore, recent advancements in the software have reduced computational costs and expanded capabilities for modeling complex microstructures found in additively manufactured alloys. As noted by Dr. Mark Thompson, Chief Technology Officer at Boeing, these improvements make the toolkit particularly beneficial for aerospace applications that demand high-performance, fatigue-resistant materials. Thompson asserts, "The use of digital twins in material qualification is a game-changer, allowing us to optimize our designs before committing to extensive physical testing."
The implications of these advancements are profound. By utilizing predictive modeling and targeted experimental data, manufacturers can determine minimum fatigue properties with fewer tests, thereby accelerating the certification process. This methodology has already shown success in the rapid qualification of innovative materials like Ferrium M54, which was quickly approved for military applications due to its fatigue resistance.
Despite these advancements, the transition to digital twin methodologies is not without challenges. Traditionalists in the aerospace industry may express skepticism regarding the reliability of simulation data compared to empirical testing. Dr. Emily Carter, a leading expert in aerospace engineering at the Massachusetts Institute of Technology (MIT), argues that while digital twins offer significant potential, they must be validated through rigorous testing to gain full acceptance in the industry.
Looking ahead, the integration of digital twins and ICME in the aerospace sector is poised to foster greater adoption of advanced manufacturing technologies, particularly in the realm of additive manufacturing (AM). As the industry grapples with the increasing demand for lightweight and high-performance materials, the ability to rapidly qualify materials will be crucial. The ongoing refinement of these digital methodologies will not only enhance the efficiency of qualification processes but also contribute to the overall safety and reliability of aerospace components.
In conclusion, the implementation of QuesTek's digital twin technology represents a significant evolution in the qualification of fatigue-critical components in aerospace. As the industry moves towards more advanced materials and manufacturing techniques, embracing these innovative approaches will be essential for meeting regulatory requirements while maintaining high safety standards. The future of aerospace qualification lies in the efficient synergy between traditional testing methods and cutting-edge computational technologies.
Advertisement
Tags
Advertisement