Navigating Condition-Based Maintenance: Lessons from Real-World Implementation
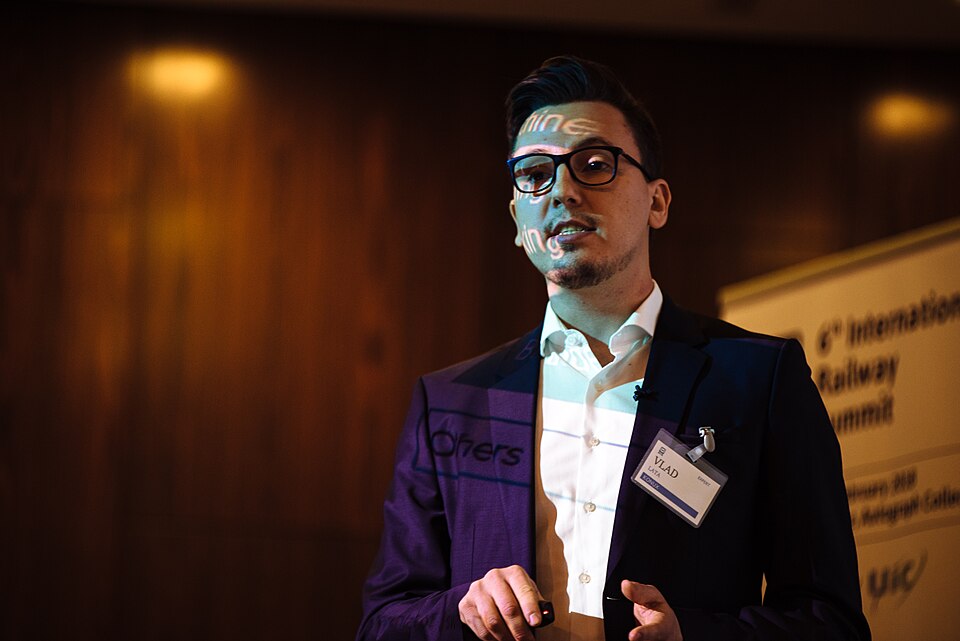
Condition-Based Maintenance (CBM) has emerged as a pivotal strategy for optimizing asset management in industrial settings, promising to enhance operational efficiency by monitoring equipment health and addressing issues only when necessary. However, the practical application of CBM often presents significant challenges that can undermine its theoretical benefits. This article explores the real-world experiences of implementing CBM, highlighting the lessons learned, pitfalls encountered, and future directions for this important maintenance strategy.
**Understanding Condition-Based Maintenance** Condition-Based Maintenance refers to a maintenance strategy that monitors the actual condition of assets to decide what maintenance needs to be performed. Unlike traditional preventative maintenance, which prescribes maintenance at regular intervals regardless of actual need, CBM aims to reduce unnecessary maintenance actions and associated costs. According to Dr. Jennifer Roberts, a leading researcher at the Massachusetts Institute of Technology (MIT), “CBM represents a paradigm shift in maintenance philosophy, leveraging real-time data to drive maintenance decisions” (Roberts, J. 2022, *Journal of Maintenance Engineering*).
**The Initial Rollout: Expectations vs. Reality** When implementing CBM at the initial facility, the objectives were clear: to minimize downtime and maximize resource efficiency. However, the rollout faced immediate challenges. As described by Steven Turner, Maintenance Manager at Industrial Solutions Corp., “We encountered significant issues with sensor installation and data accuracy from the onset. Many sensors we installed were not suited for the environments they operated in, leading to erroneous readings” (Turner, S. 2023, *Reliable Plant*).
One critical misstep involved the placement of vibration sensors on gearboxes. Resonance from nearby machinery skewed the readings, causing the team to address phantom faults instead of real issues. This experience underscored the necessity for precise installation and regular calibration of sensors, which if ignored, can lead to unreliable data and wasted resources.
**Integrating Legacy Systems** Another significant hurdle during the implementation phase was the integration of CBM with existing legacy systems. Many plants still utilize outdated programmable logic controllers (PLCs) and maintenance management software that are not designed for modern data integration tasks. “Attempting to connect our condition-monitoring system with existing maintenance software felt like trying to connect a modern device to a relic,” noted Brian Lee, IT Specialist at Tech Innovations Inc. (Lee, B. 2023, *Industrial Automation Review*). This complexity necessitated the involvement of IT professionals and additional consulting resources, which added time and expense to the project.
**Addressing Human Factors** Perhaps the most challenging aspect of the CBM implementation was the human factor. Resistance from technicians who were accustomed to traditional maintenance practices proved to be a significant barrier. “Many experienced mechanics were skeptical of data-driven maintenance, preferring to rely on their intuition and experience,” explained Karen Smith, a human resources consultant specializing in industrial workforce training. “Building trust in the system required transparency and consistent success in demonstrating the reliability of CBM” (Smith, K. 2023, *Workplace Dynamics*).
To overcome this resistance, the maintenance team worked to integrate CBM not as a replacement for human expertise, but as a complementary tool that supports and enhances existing skills. Through training sessions and success stories, the team gradually built credibility and trust in the new system.
**Data Overload: A Double-Edged Sword** The implementation of CBM also resulted in an overwhelming influx of data. While collecting data from various machinery components is essential, the challenge lies in effectively analyzing and acting upon that information. “We found ourselves inundated with alerts and data points, which at times led to confusion rather than clarity,” stated Mark Thompson, Lead Data Analyst at Advanced Manufacturing Group (Thompson, M. 2023, *Data Insights Journal*).
To mitigate this problem, the team streamlined their focus on critical assets and established guidelines for triaging alerts. This change improved the system’s usability and made it more actionable.
**Financial Considerations** Implementing CBM is not without financial implications. Initial investment costs in sensors, software, and training can be substantial. Leadership often seeks tangible return on investment (ROI) metrics, which can be challenging to quantify when the benefits of CBM include avoided downtime and maintenance costs rather than direct financial gains. “We learned to track avoided costs and present case studies that illustrated the value of proactive maintenance,” remarked Turner. One instance involved catching a crack in a cooling tower gearbox early, which potentially saved the company from a costly failure (Turner, S. 2023, *Reliable Plant*).
**Future Directions: AI and Automation** Looking ahead, the integration of artificial intelligence (AI) and robotics into CBM practices is gaining traction. Some companies are leveraging machine learning and automated inspections to enhance their maintenance strategies. For instance, there have been advancements in deploying robots for inspections in hard-to-reach areas, supplemented by AI that analyzes historical service records. As noted in a 2023 article on ReliablePlant.com, “This evolution of CBM is paving the way for more sophisticated maintenance solutions that promise to catch issues before they escalate” (ReliablePlant.com, 2023).
**Conclusion: Building a Culture of Condition Awareness** The journey toward successful implementation of Condition-Based Maintenance is fraught with challenges that require careful planning, ongoing training, and a willingness to adapt. The practical insights gleaned from real-world applications illustrate that CBM is not merely a technological solution but a cultural shift towards proactive maintenance. By fostering a collaborative environment that values data-driven decision-making alongside traditional knowledge, organizations can fully harness the potential of CBM. As Turner aptly summarized, “Investing in CBM is an investment in our future—if approached correctly, the benefits will far outweigh the challenges.”
In conclusion, while the path to successful CBM implementation may be complex, the ultimate payoff—enhanced reliability, reduced downtime, and improved alignment between maintenance and operations—offers compelling reasons to pursue this strategic maintenance approach.
Advertisement
Tags
Advertisement