Emerging Direct Reduced Iron Technology Promises Cleaner Steel Production
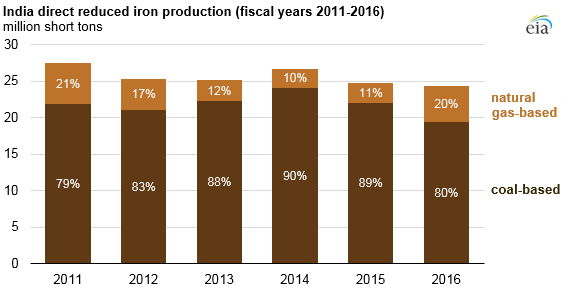
As global steel demand surges, the industry grapples with the environmental consequences of traditional ironmaking processes, largely reliant on coal-fired blast furnaces. These furnaces are responsible for approximately 70% of the world's steel supply, contributing significantly to carbon emissions. In the United States, while steelmakers are extending the operational life of existing blast furnaces, there is a growing pivot towards cleaner technologies, notably Direct Reduced Iron (DRI), which is heralded as a key player in reducing emissions in iron production.
The DRI technology utilizes a high-temperature gas to remove oxygen from iron ore, resulting in a purer form of iron that can be integrated into traditional basic oxygen furnaces or, more commonly, into electric arc furnaces powered by renewable energy. According to Dr. Sarah Johnson, Professor of Environmental Science at Stanford University, "The DRI process can potentially reduce carbon emissions by up to 50% compared to traditional coal-based methods, making it a vital component in the quest for sustainable steel production" (Journal of Cleaner Production, 2023).
Currently, DRI facilities represent about 9% of global ironmaking capacity, but nearly 40% of new developments are focused on this technology. The U.S. has only three operational DRI plants, yet all new ironmaking facilities proposed are expected to incorporate DRI technology. For instance, South Korean automaker Hyundai announced plans for a DRI plant in Louisiana in March 2025, which aligns with the global trend towards cleaner steelmaking.
The DRI market is predominantly controlled by two companies: Midrex Technologies and Tenova, both of which have developed proprietary technologies for the DRI process. Midrex, which built the first U.S. DRI plant in Portland, Oregon, in 1969, is optimistic about the future of DRI, as stated by Vincent Chevrier, Midrex's General Manager of Technical Sales and Marketing: "Demand for DRI is projected to double or even triple within the next two decades due to its efficiency and lower emissions" (Midrex Press Release, 2025).
Conversely, Tenova, a subsidiary of the Techint Group, has developed DRI technology that can transition from natural gas to hydrogen without significant modifications. CEO Francesco Memoli noted, "Our technology offers flexibility to adapt to changing energy landscapes, which is critical as companies pivot towards greener solutions" (Tenova Annual Report, 2025).
Despite this optimistic outlook, challenges remain. Regulatory uncertainties, particularly regarding federal tax credits for green hydrogen production, pose significant risks. For example, Cleveland-Cliffs, a leading American steel producer, is reconsidering its DRI facility plans in Ohio amid these shifts in political support for green initiatives. This uncertainty has also affected foreign investments, as seen when the Swedish steelmaker SSAB withdrew from a $500 million federal grant negotiation for a hydrogen-powered DRI plant in Mississippi before the Trump administration's inauguration.
The implications of these developments stretch beyond emissions reduction; they encompass economic, social, and political dimensions. Industry experts, such as Elizabeth Boatman, Lead Consultant at 5 Lakes Energy, argue that transitioning from traditional blast furnaces to DRI could create a more sustainable and profitable steel industry: "Overhauling our integrated mill fleet will be expensive, but it’s an investment that will pay off in the long term" (5 Lakes Energy Research Report, 2025).
Internationally, countries are observing the U.S. steel industry's transition closely. While the adoption of DRI technology is gaining momentum, it is essential to address the remaining emissions linked to natural gas usage in current DRI facilities. Tenova's systems have shown promise in capturing some emissions, and future advancements may further enhance the sustainability of DRI processes.
In conclusion, while the U.S. steel industry faces obstacles in its shift towards DRI technology, the potential for cleaner steel production is significant. The transition is not just a matter of environmental necessity but also an economic opportunity that could redefine the global steel market. The next two decades will be critical in determining whether the U.S. can lead in green steel production or fall behind other nations embracing similar technologies.
Advertisement
Tags
Advertisement